For many years it has been the case that, when creating a floor, it has first been necessary to ensure that the subfloor is as level as it can possibly be, and traditionally this has been done by adding a layer of screed on to the concrete. A concrete substrate is never going to be level enough to lay tiles directly, and it is not advisable to lay other final flooring surfaces without first adding a screed, although there is no regulation which says that you have to have one. However, if you don’t, there is a risk that the final flooring, especially if it is tile, could become damaged or cracked simply because the substrate is not flat.
Traditional screed is made from a mix of sand and cement and laid in a thin layer by hand. This is better than trying to install the floor directly on to concrete but is still unlikely to achieve maximum level of the measurement SR1 (Surface Regularity 1). This allows for only 3mm deviation from perfectly flat across the whole floor and is referred to as high standard. Normal standard is SR2 and allows for 5mm deviation, while SR3 is utility standard and allows for up to 10mm deviation. A sand and cement screed laid by hand is unlikely to be better than SR3.
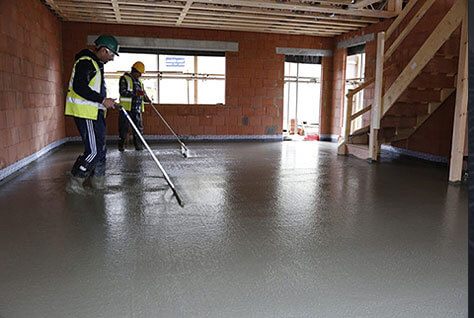
On the other hand, the liquid screeds that we lay at UK Screeds will achieve SR2 as a minimum and are usually at SR1. These screeds are also known as self-levelling screeds, floor levelling compounds, anhydrite screeds, and more. The surface regularity is measured by placing a 2-metre long straightedge flat on the surface and resting under its’ own weight. The deviation of the screed from the underside of the straightedge is then measured using a slip gauge.
Surface regularity or flatness of a screed is one of the factors that determine the serviceability of a floor. Flaws in surface regularity can be the cause of trip hazards, increased wear, aesthetic issues, and excessive sway of wheeled traffic, and can also lead to difficulties in the installation of equipment specified for the floor.
This is why more and more specifiers are insisting on the use of floor levelling compound instead of sand and cement. Because it is in liquid form it will fill any gaps, and this is most important when underfloor heating is being installed. When using sand and cement screed there will almost certainly be air pockets, and these have an effect on the transfer of heat from the pipes into the room.
Furthermore, the thermal heat transfer properties of our liquid floor compound in Oxford, or wherever your project happens to be, are nearly twice that of sand and cement. This means that less energy is required to heat the room. Our floor compound can also be laid more thinly than a sand and cement screed, which is a further benefit when it comes to the amount of energy required for heating. That translates into cost savings for the life of the building and, of course, is more environmentally friendly as well.
Another advantage of our liquid floor compound is that it is far faster to lay. We deliver it to site pre-mixed and it is then poured into position using a long hose and a pump. Our teams can lay 100 square metres in 45 minutes or so, and as much as 2,000 square metres in a day. This is nearly 20 times as fast as laying a sand and cement screed by hand!
Furthermore, our liquid screed will be dry enough to walk on and take light traffic in 48 hours or less. This means that it won’t cause unreasonable delays to other contractors who have to work on the site.
A further advantage of liquid screed is that it doesn’t curl and there is minimum shrinkage. That means that it can be force dried in order to reduce the amount of time before the final flooring surface can be fitted. Screed drying times holding up a project can be a big issue for contractors, and penalty clauses for running over time can run into a considerable amount of money, so using force drying can reduce the overall drying time by as much as two thirds.