When constructing a new building, or carrying out a major renovation, one of the most important considerations is the floor. It may seem obvious, but everything and everybody is going to be standing or walking on that floor and it has to be both safe and sound, and level.
That latter point is vital. It is a fact that the most common accidents that occur everywhere and anywhere are slip and fall accidents. While these may be from working on a building site at height and, say, slipping from scaffolding, the majority are on floors. This can be for a number of different reasons, such as the material from which the floor is constructed. Some floor surfaces are simply more slippery than others.
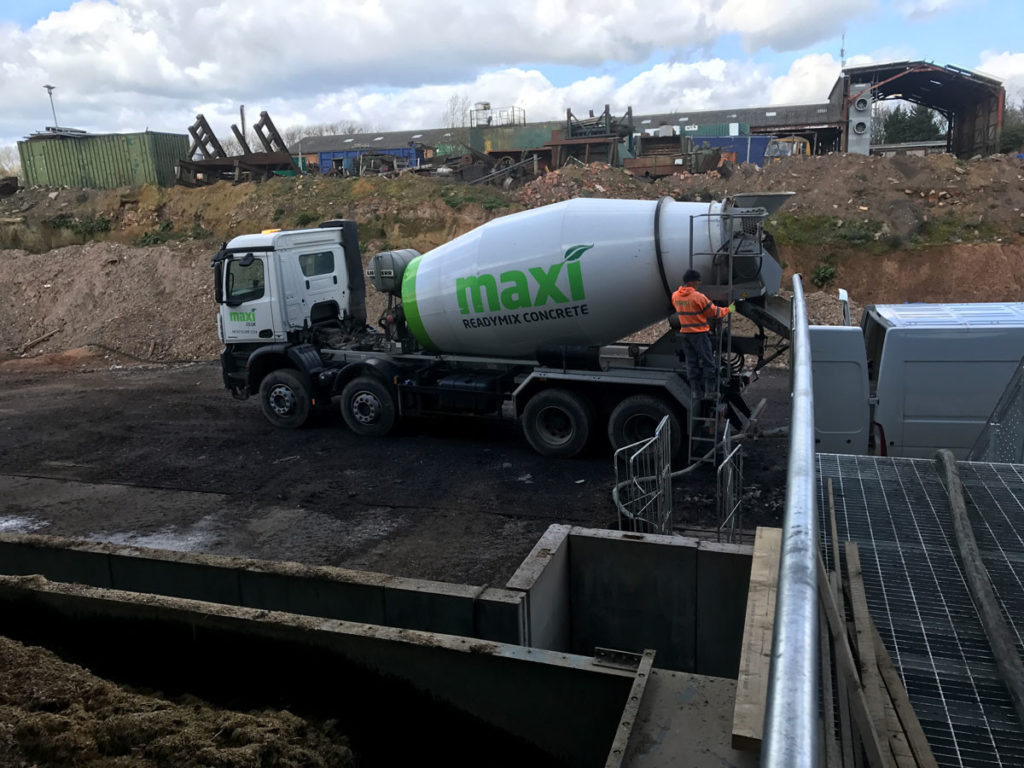
However, there can be all sorts of other problems with floors such as carpets which have holes or rips in them, wood floors where floorboards have become loose over time, spills which have not been mopped up, and floors which are not flat and have bits which can cause trips, and equally importantly, floors which have an uneven underfloor and which result in the final flooring finish becoming loose – such as in tiling.
For instance, if the substrate is not level and tiling is laid directly on to it, then as people walk over it the tiles can work loose because one end of the tile is lower than the other end. That can cause the tile to rise at the other end which can result in someone tripping over it. It happens all too often.
That is why, whatever the final flooring is going to be in a building, the underfloor on which it is to be laid must be as flat and level as humanly possible. And that is why a screed is essential. What this does is to produce a level surface over the concrete substrate so that the final flooring can be fitted in a safe and correct manner.
This is what Wikipedia has to say about screed: “In the UK, screed has also come to describe a thin, top layer of material (sand and cement, magnesite or calcium sulphate), poured in site on top of the structural concrete or insulation, on top of which other finishing materials can be applied, or the structural material can be left bare to achieve a raw effect.”
As can be seen, a screed can be made of various materials, and traditionally it has been simply sand and cement. Even that definition is not entirely accurate since it uses the term “poured”. Traditionally a sand and cement screed has been mixed on site in a cement mixer and then barrowed on to the substrate and levelled out by a labourer on his hands and knees using a trowel.
True, today, we have sand and cement screeds which are mixed off site and contain minerals to delay it setting so that it can be used all day, and a cement screed can now be produced in liquid form and poured on.
But even so, the anhydrite screed which we install at UK Screeds is becoming used more and more because it is just so much better than the alternatives. It is particularly useful when used in conjunction with underfloor heating. This is because it completely covers the heating pipes. When you use a traditional sand and cement screed it is almost impossible to cover the heating pipes completely, so there are gaps which affect the transfer of heat into the room. Not only that, but the actual materials of which an anhydrite screed in Reading – or anywhere else – is made have almost twice the thermal transfer properties of a sand and cement screed.
So not only do you get complete coverage of the heating pipes, but you also get nearly double the thermal transfer. This means that less energy is needed to heat the room to the same temperature and that results in a continuing saving on energy costs for as long as the building lasts.
There are other benefits too, not the least of which is that an anhydrite screed will always be more level than traditional sand and cement and so will be far safer as far as the finished floor is concerned, especially when that flooring has to be glued to the screed as tiles do.