There is no doubt that liquid screeds are making great inroads into the world of floor screeds because they have so many advantages over the traditional sand and cement. In fact, one supplier recently stated that around 25% of all screeds laid are now liquid screeds, either anhydrite or cement based.
At UK Screeds we have been providing anhydrite liquid floor screeds for contractors and homebuilders for approaching 15 years now, and we have no less than ten branches in England and Wales, so we can provide the service wherever you are in the two countries. We are also in the process of expanding into Scotland and Northern Ireland, so will shortly be covering the whole of the UK.
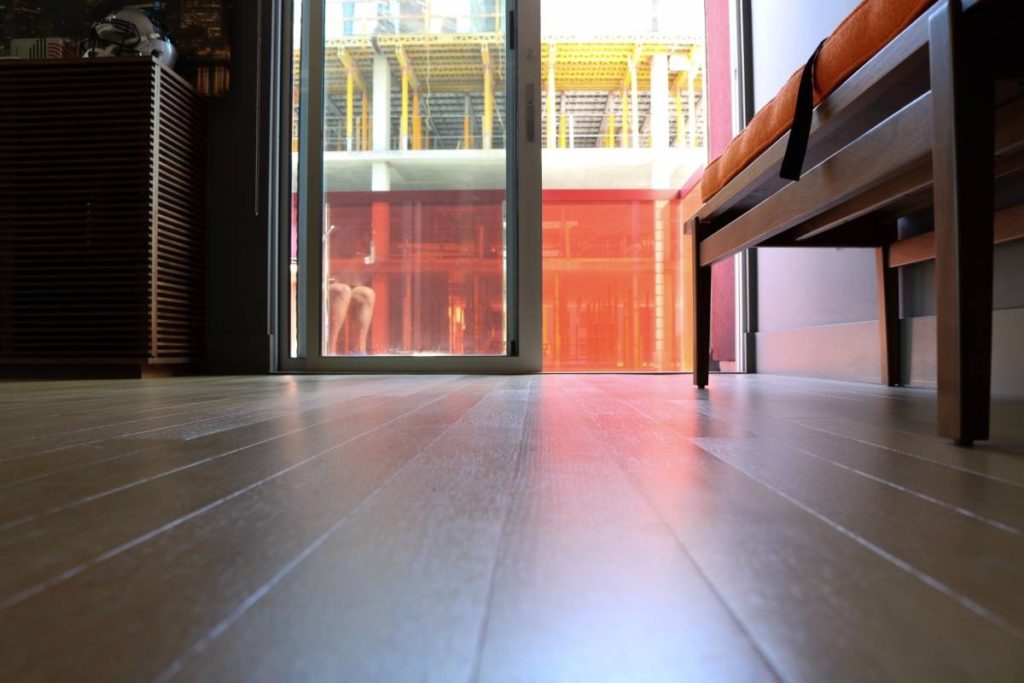
Our liquid screeds can be laid far faster than sand and cement – in fact, anything up to 20 times faster – which means that there is a huge saving on labour. They also dry to the point of being safe to walk on within 24 – 48 hours. Those two things alone mean that there are no hold-ups to other contractors who need to work on the site, and as you know, in contracting, time is money.
Liquid screeds can be laid far thinner than sand and cement, so there is also a saving on the actual materials used. They are the perfect solution when underfloor heating is going to be installed as well. There are a couple of factors here, one of which is that because our screeds are liquid, they will completely cover the heating pipes without leaving any gaps or voids. That is almost impossible to achieve with a traditional sand and cement screed laid by hand.
The second point is that anhydrite screed has a thermal heat transfer rating which is close to double that of sand and cement, which means that less energy is required to heat the room to the same temperature. That means ongoing cost-savings for the occupier of the building and also makes the screed more environmentally friendly. On that note, some 35% of anhydrite screed consists of recycled material as well.
However, as with any screed, you do need to take some precautions before adding the finishing floor surface, especially when tiling.
Looking at the technicalities, anhydrous screeds contain anhydrous (dry) calcium sulphate and aggregates instead of a cement binder. The binder may also be alpha hemi-hydrate which is a stronger crystalline form. When water is added, the binders become calcium sulphate dihydrate, which is known as gypsum. This reaction stops when most of the calcium sulphate binder is used up and is generally completed in 3 – 7 days, leaving the remaining water to dry out through the surface.
This means that, when tiling on to an anhydrite screed in Bristol, or anywhere else, it is essential to ensure that the screed is dry enough. Typical values quoted for impermeable floors are less than 0.5% water by weight or less than 75% relative humidity. The water by weight figure may be less than 1% for more permeable floor finishes.
Drying times for anhydrite screeds are calculated at one day per mm up to a depth of screed of 40mm and two days per mm thereafter. This assumes that the air temperature is 20°C and the relative humidity is no greater than 65%. In practice, in the UK it is unlikely that these figures would be maintained over the whole drying time, so the actual time is likely to be longer.
However, it is possible to use force drying. Once the screed has been laid for at least seven days, the underfloor heating can be switched on and increased by 5°C per day until the maximum required working temperature is reached, or per the underfloor heating manufacturer’s instructions. This is maintained for at least seven days and then gradually reduced to 15 – 20°C. A temperature of 55°C should not be exceeded. Dehumidifiers could also be used in addition.
Before the tiling is laid, it is necessary to remove the layer of laitance that forms on the surface of the screed during the first week or so. This is done by sanding after 7 – 10 days. It should not be left longer than this because the laitance will harden and become more difficult to remove.
Before tiling, it is recommended that a primer should be applied to the surface of the screed. When considering the adhesive to be used it is also necessary to take into consideration the type of tile to be used and, in addition, the type and method of cleaning the finished floor – in particular how wet it may become when in use.