Many of us tend to think of underfloor heating as a new system but believe it or not it dates back at least 7,000 years! Back in the day, they had trenches cut into the floors with stones laid over the top of them and they were heated by fires in strategic positions.
Things have certainly changed a lot in the intervening period, but the overall principle remains the same. Today we have modern underfloor heating systems that can be operated by electricity or by heat from an air source or ground source heat pump. Yes, we can extract heat from the air or heat from the ground which is both environmentally friendly and more economic.
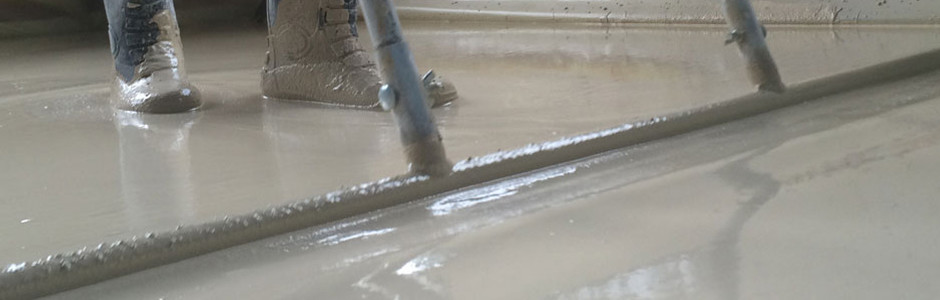
However, probably the biggest improvement with underfloor heating systems has been the quite recent introduction of liquid screeds. The most common of these today is liquid gypsum screed which is created using calcium sulphate. These are also known as flowing screeds, floor compounds, and anhydrite screeds, but are all the same thing. Anhydrous calcium sulphate becomes gypsum when it absorbs water.
The liquid anhydrite screeds that we install at UK Screeds have several advantages over the traditional sand and cement screed. First of these is the speed of laying. A traditional sand and cement screed is mixed on site in a concrete mixer, barrowed in to the property, and then laid by hand by a worker on his hands and knees using a trowel. Each batch of screed will be slightly different from the next depending how much sand and cement and water is added to the cement mixer.
By contrast, when carrying out floor preparation in Essex, for example, our liquid screed is delivered to site ready mixed and poured on to the concrete substrate using a pump and hosepipe direct from the delivery vehicle. Compared with laying sand and cement, this is unbelievably fast, which can be of considerable importance on any building project. Time is money, and our teams can lay as much as 2,000 square metres in a day which is around 20 times as fast as laying sand and cement by hand.
Furthermore, the screed will be dry enough to walk on in 24 – 48 hours which means that it will not delay other workers on site.
Our liquid screeds have a huge advantage when it comes to installing underfloor heating. We also undertake the installation of underfloor heating using pipes which will have water pumped through them that has been heated by a heat source – which could be a boiler, or an air-source or ground-source heat pump. Because the screed is liquid it totally envelops the heating pipes leaving no gaps, which means that heat transfer into the room is 100% even. When a traditional screed is laid by hand it is almost impossible to cover the heating pipe without leaving gaps, so the heat transfer is not even.
Furthermore, a gypsum screed has heat transfer properties which are nearly twice those of sand and cement. In addition, our liquid screeds can be laid thinner than sand and cement which saves on materials and also means that the room will heat up faster. Overall, there will be a considerable saving on ongoing energy costs.
Our screeds are pretty much self-levelling, but we use lasers in order to get the screed as flat as possible. This means that we always achieve Surface Regularity 2 (SR2), but usually SR1 – and that is as level as you can get. This is vital when laying flooring such as tiles.
Screed drying times are also an issue for contractors. Penalty clauses and site running costs for running over time on a contract can run into considerable amounts of money. The drying times before the final flooring can be installed are usually based on a level environment of 20°C and 60% relative humidity over the whole of the drying period, but in reality this is unlikely to occur in the British climate.
Typically, our liquid screeds installed at a depth of 50mm will be said to have a drying time of 60 days, but this may well be longer depending on temperature and humidity.
However, our screeds can be force dried using the appropriate equipment, and this can bring the drying time down to four weeks – 28 days – saving a considerable amount of time before the final flooring can be laid. On any contract, time is money, so this can bring a considerable saving for developers and contractors and adds confidence that the construction project will be completed on time.